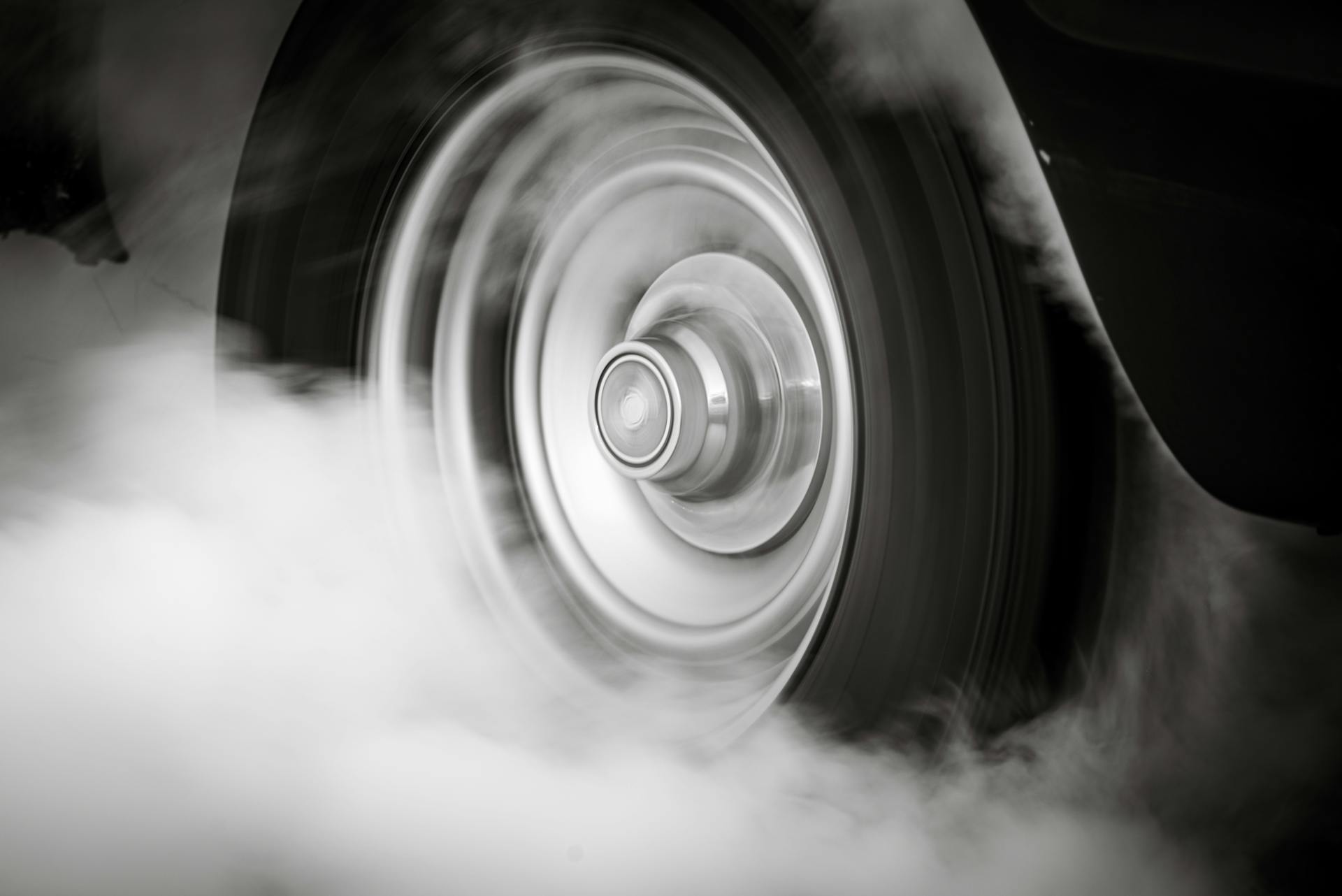
Synchronous speed is the speed at which an AC motor operates in synchronization with the frequency of the electrical supply. This speed is determined by the number of poles in the motor.
The synchronous speed of a motor is calculated using the formula: Speed = (120 x Frequency) / Number of poles. For example, a motor with 4 poles operating at a frequency of 50 Hz will have a synchronous speed of 1500 rpm.
A motor's synchronous speed is critical in determining its working characteristics.
For more insights, see: What Is Synchronous Speed
Types of Synchronous Speed
Synchronous speed can be categorized into two main types: nominal synchronous speed and slip synchronous speed.
Nominal synchronous speed is the speed at which an induction motor operates when it's perfectly synchronized with the AC supply frequency.
Slip synchronous speed, on the other hand, is the speed at which an induction motor operates when it's not perfectly synchronized with the AC supply frequency.
Slip synchronous speed is always lower than the nominal synchronous speed.
Here's an interesting read: Permanent Magnet Synchronous Generator
Why Synchronous Speed is Required
Synchronous speed is a fundamental concept in electrical engineering, especially in relation to alternating current (AC) motors. It refers to the speed at which the magnetic field created by the motor's stator rotates.
This speed is determined by the frequency of the power supply and the number of poles in the motor. Matching Power Supply Frequency is crucial for the motor's efficiency and performance.
If the motor operates at a speed significantly different from its synchronous speed, it can experience efficiency losses and overheating. Maintaining Efficiency requires AC motors to operate at or near their synchronous speed for optimal efficiency.
Synchronous speed is linked to the motor's ability to deliver torque effectively. If a motor operates below synchronous speed, it may not produce the required torque for its intended applications.
In power generation, synchronous speed is critical for generators. It ensures that the generator rotates at the same speed as the grid frequency, maintaining the synchronization needed for the power grid's stability.
You might like: Asynchronous Generator vs Synchronous Generator
Here are the reasons why synchronous speed is required:
- Matching Power Supply Frequency
- Maintaining Efficiency
- Maintaining Proper Torque
- Frequency Control in Power Generation
- Industrial Applications
In various industrial processes where precise speeds are required, synchronous motors are used for their ability to operate consistently at their synchronous speed. These motors find applications in industries such as manufacturing, robotics, and precision machinery.
Motor Working Principle and Characteristics
A synchronous motor works on the principle of magnetic locking between the stator RMF and the rotor magnetic field. This magnetic locking causes the rotor to rotate at the same speed as the stator RMF, which is called the synchronous speed.
The synchronous speed is determined by the formula NS = 120f / p, where f is the input frequency and p is the number of poles. For example, if the input frequency is 50 Hz and the number of poles is 4, the synchronous speed would be 1500 rpm.
The characteristic of a synchronous motor is represented on a two-dimensional graph, with the X-axis representing speed and the Y-axis representing torque. This graph shows the dependency between speed and torque, and multiple lines are shown to represent different operating conditions.
The synchronous motor's speed is independent of the load, but it will stall if the torque increases beyond the breakdown torque. The breakdown torque is the maximum available torque the motor can provide, and it's an important characteristic to consider when designing a synchronous motor system.
Here's a quick summary of the synchronous motor's characteristics:
- Speed only varies with the frequency of the input supply
- Speed is independent of the load
- Will stall if torque increases beyond the breakdown torque
- Can run in both leading and lagging power factors
Reluctance
Reluctance motors have a solid steel cast rotor with projecting toothed poles.
Typically, there are fewer rotor poles than stator poles to minimize torque ripple and prevent the poles from all aligning simultaneously.
The size of the air gap in the magnetic circuit and thus the reluctance is minimum when the poles align with the stator's magnetic field.
This creates torque that pulls the rotor into alignment with the nearest pole of the stator field, a position that cannot generate torque at synchronous speed.
The machine thus starts as an induction motor until it approaches synchronous speed, when the rotor "pulls in" and locks to the stator field.
Small reluctance motors have low torque and are generally used for instrumentation applications.
Moderate torque, multi-horsepower motors use squirrel cage construction with toothed rotors.
Reluctance motor designs have ratings that range from fractional horsepower (a few watts) to about 22 kW.
Hysteresis
Hysteresis motors have a solid, smooth, cylindrical rotor made of high coercivity magnetically "hard" cobalt steel.
This type of material has a wide hysteresis loop, requiring a high magnetic field to reverse magnetization once it's magnetized in a given direction.
The rotating stator field causes each small volume of the rotor to experience a reversing magnetic field, resulting in a phase lag behind the applied field.
This lag produces torque as the rotor tries to "catch up" with the stator field.
The rotor's axis of magnetic field lags behind the stator field's axis by a constant angle δ, creating torque.
The rotor has a 2-pole low reluctance bar structure.
As the rotor approaches synchronous speed and slip goes to zero, it magnetizes and aligns with the stator field, causing the rotor to "lock" to the rotating stator field.
A major advantage of the hysteresis motor is that it develops constant torque from startup to synchronous speed, making it self-starting.
Hysteresis motors are manufactured in sub-fractional horsepower ratings, primarily as servomotors and timing motors.
They are more expensive than reluctance type motors, but are used where precise constant speed is required.
Working Principle
A synchronous motor works on the principle of magnetic locking between the stator RMF (rotating magnetic field) and the rotor magnetic field. This principle is based on the fact that opposite poles attract each other.
The stator RMF is generated by a three-phase AC supply, while the rotor's magnetic field is created by a DC supply. This dual excitation allows the rotor to rotate at the same speed as the stator RMF.
The synchronous speed of the motor is determined by the input frequency and the number of poles in the stator and rotor. It can be calculated using the formula NS = 120f / p.
The rotor's magnetic field is fixed, and its poles interact with the stator RMF, rotating at the same speed as the synchronous speed. If the rotor rotates at the same speed as the stator RMF, there is no load torque.
The motor's behavior changes when a mechanical load is applied, causing the rotor to oscillate and develop torque. This phenomenon is known as 'hunting'.
Representation of Motor Characteristics
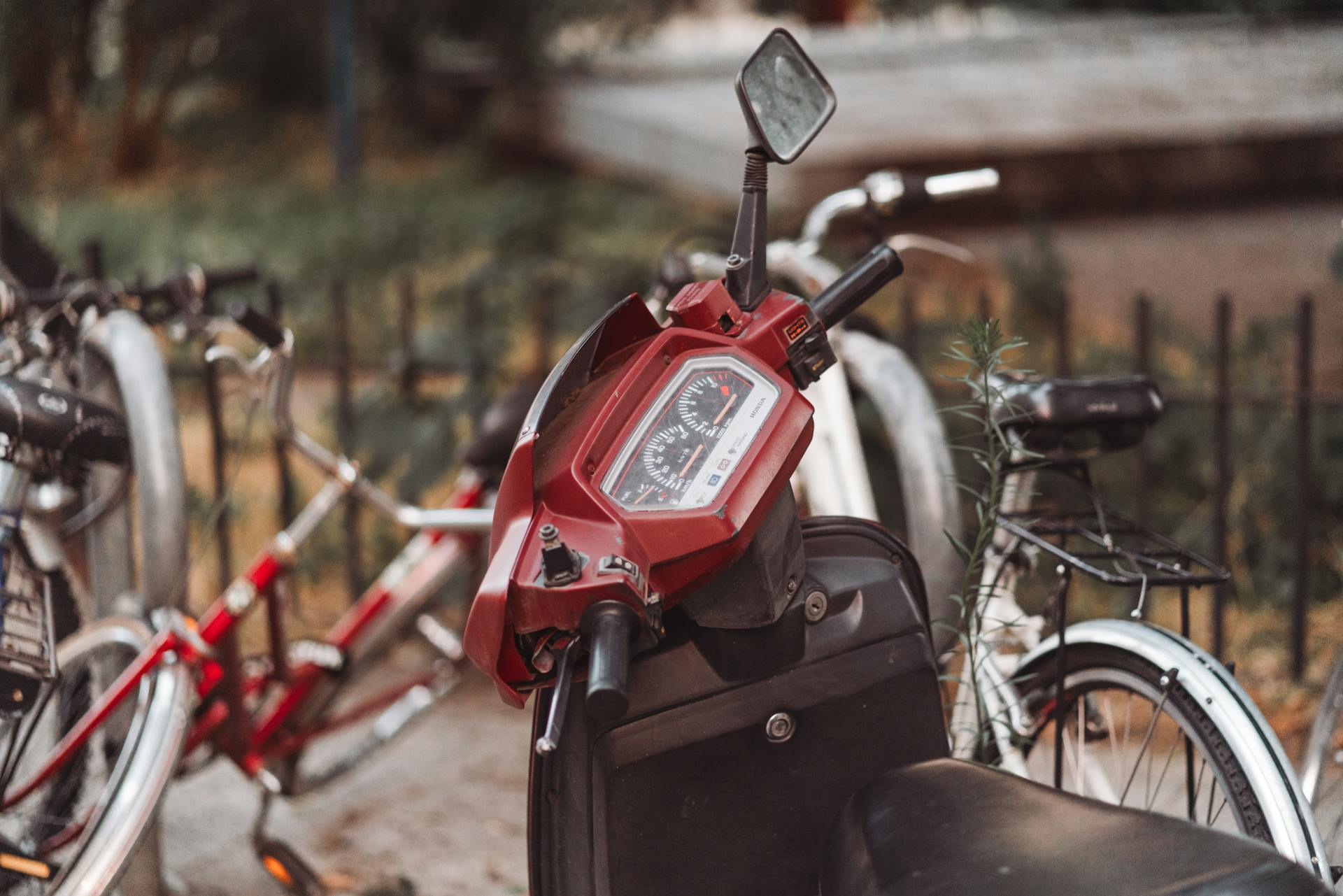
The representation of motor characteristics is a crucial aspect of understanding how motors work. A two-dimensional graph is commonly used to represent the characteristic of a synchronous motor, with the X-axis representing speed and the Y-axis representing torque.
This graph clearly shows the dependency between physical variables, allowing for a clear presentation of the motor's behavior. Several lines are often shown, representing different operating conditions and modes.
The type of operation and temperature are key factors that influence the characteristics of a synchronous motor, resulting in different lines on the graph. The graph for the DSD2-132YZ54A(R)-20-5 synchronous motor shows the variations in speed and torque under different conditions.
By analyzing the graph, you can gain a deeper understanding of how the motor responds to different operating conditions and temperatures. This information is essential for selecting the right motor for a specific application.
Pony Motor Method
A pony motor is a small induction motor or DC shunt motor that is connected with the shaft of a synchronous motor.
It helps in providing the necessary starting torque to the synchronous motor.
The DC excitation is not applied until the rotor attains speed near synchronous speed.
This allows the rotor to magnetically lock with the rotating magnetic field (RMF).
The power supply to the pony motor is cut off once the rotor is synchronized with the RMF.
Frequently Asked Questions
Is synchronous speed the same as rpm?
Synchronous speed is not exactly the same as RPM, as actual RPM is typically 3 to 5% lower. Check Table 7-1 for a detailed comparison of synchronous speed and actual speed values.
What is 120 in synchronous speed?
In a 60Hz system, 120 represents the number of zero crossings per second, which determines the frequency of torque peaks and the stator's magnetic interaction with the rotor. This key value is crucial for understanding the dynamics of synchronous speed and its impact on motor performance.
Sources
- https://en.wikipedia.org/wiki/Synchronous_motor
- https://hvhindustrial.com/blog/difference-between-synchronous-and-asynchronous-motors
- https://www.wazipoint.com/2023/11/what-is-synchronous-speed.html
- https://www.baumueller.com/en/insights/basics/basics-the-synchronous-motor-characteristic
- https://www.electricaltechnology.org/2022/09/synchronous-motor.html
Featured Images: pexels.com