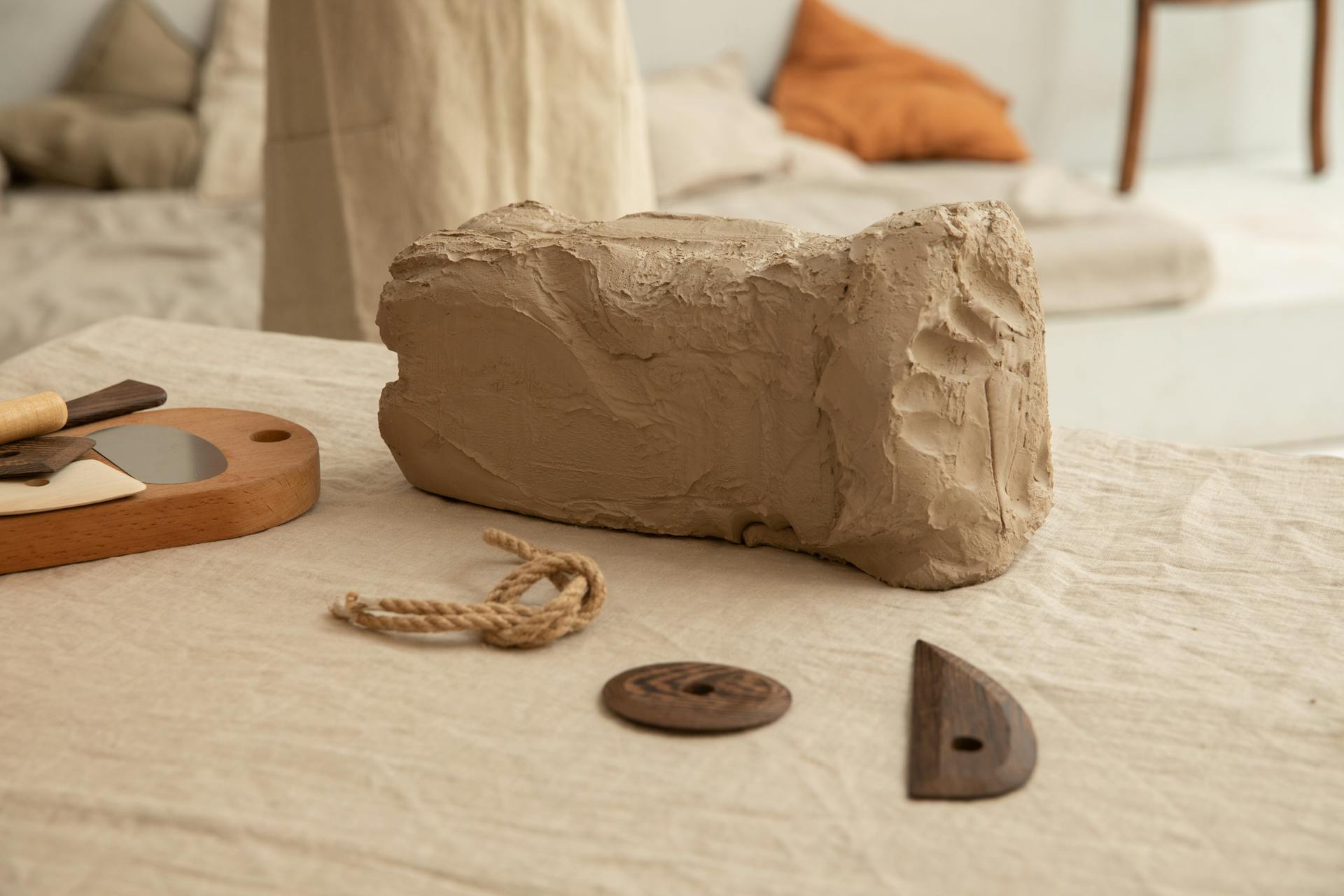
If you work in the manufacturing business, you have probably heard of the term "master production schedule" or MPS for short. A master production schedule is a detailed plan that outlines what finished goods will be produced, how much of each product will be made and when they will be produced. The master schedule details the specific dates and quantities needed to meet customer demand and prevent stockouts.
The master production schedule plays a crucial role in the success of any manufacturing business. It is used to perform effective cost control by helping businesses avoid overproduction or underproduction of goods. By maintaining an accurate MPS, manufacturers can make adjustments to their production process as needed to ensure that they are meeting customer demand while also minimizing waste.
In this complete guide, we will take a closer look at what master production scheduling is, why it is important for manufacturing businesses, and how it can be used to optimize production processes and improve profitability. Whether you are new to the concept of MPS or looking for tips on how to create an effective master production schedule, this guide has everything you need to know!
Discovering the Benefits of a Master Production Schedule
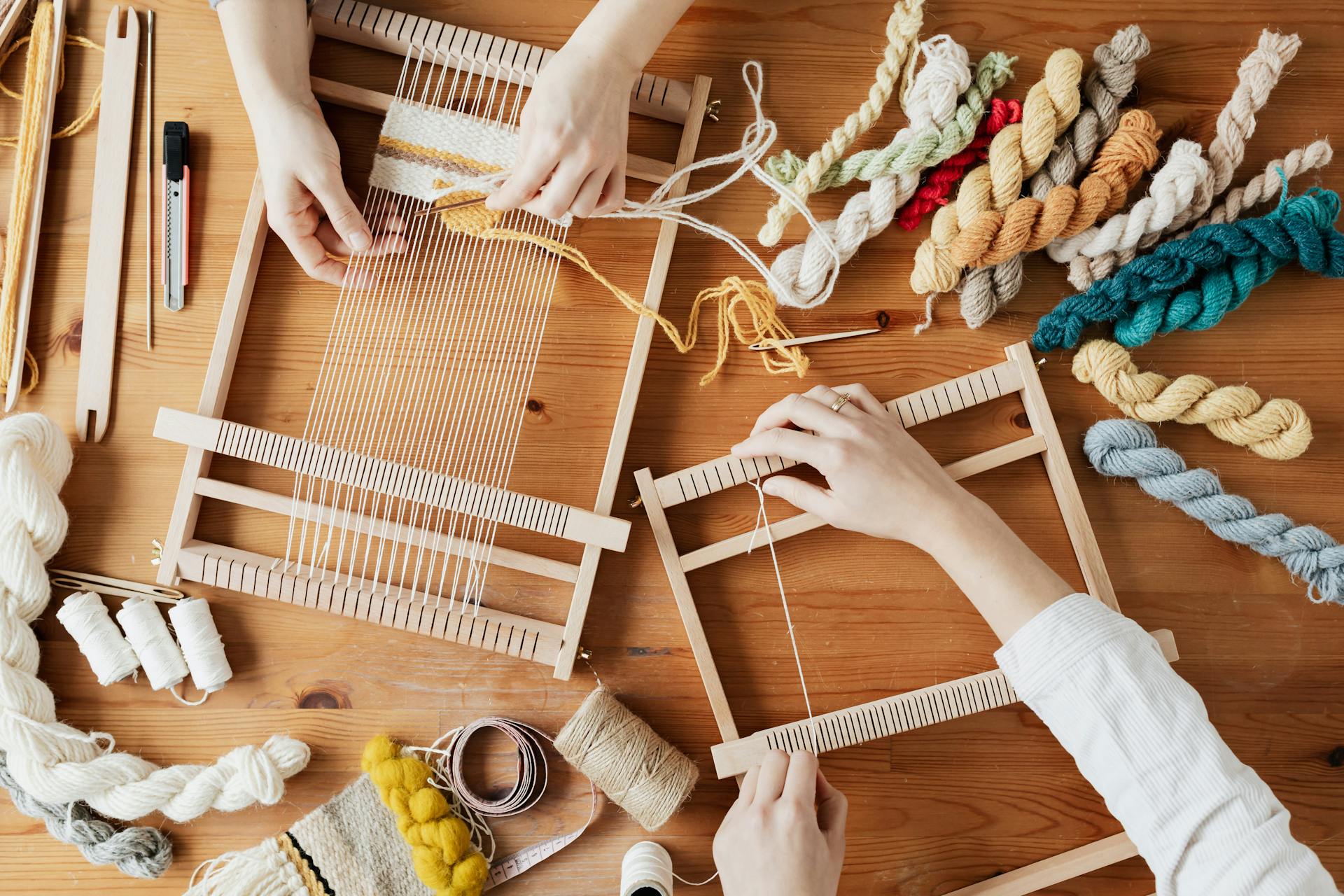
Have you ever heard of a master production schedule (MPS)? If not, let me give you a quick overview. An MPS is a centralized document telling everyone in the business including time frames for manufacturing lead time, demand plan, raw materials needed, and supply chain information. There are several master production schedule process steps you'll need to take before you're ready to create an official MPS proposal, such as creating a rough draft and using the rough-cut capacity planning technique.
The proposed MPS should be able to handle any manufacturing needs that arise in your business. It should continuously assess and adjust as necessary to meet demand while keeping customer service effective and minimizing inventory investment. The master schedule is essential on the shop floor because it provides a clear set of instructions for producing sales orders across all sales channels.
A master production schedule makes it easier for businesses to maintain forecast relationships with customers while managing inventory levels effectively. By decreasing production and supply chain costs, many businesses have found that implementing an MPS has increased efficiency and productivity. The crucial input from aggregate operations plans gives businesses the ability to create an actionable strategy for meeting their production goals.
Learn how to create an effective master production schedule
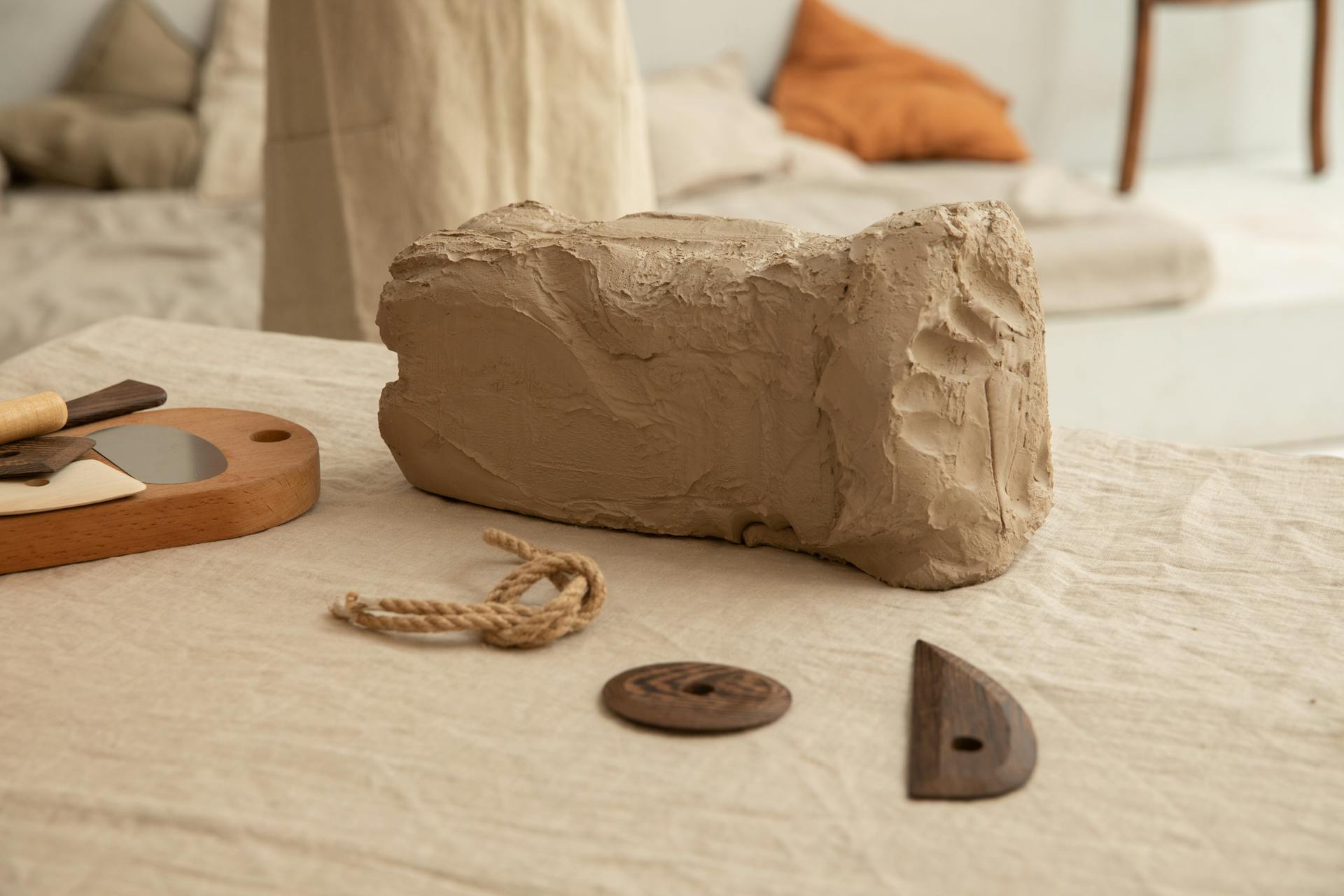
Creating an effective master production schedule is crucial for any business, especially for a leather manufacturer selling bags. A master production schedule is a comprehensive plan that outlines the production quantity needed to meet projected demand while taking into account on-hand inventory and current inventory demand. The scheduled production quantity is calculated based on several factors such as actual orders, estimated lead times, and expected demand.
A run-of-the-mill master production schedule doesn't change based on the actual orders received by the manufacturer. This can result in overproduction or underproduction of goods, which can lead to business-harming errors. To avoid this, manufacturers should use a dynamic master production schedule that takes into account any changes in actual orders received and adjusts accordingly.
The best way to create a visually appealing and accurate master production schedule is by using spreadsheet programs like Excel or specialized manufacturing execution systems (MES software). An ERP system lets businesses quickly create a master production schedule with minimal human intervention. Production scheduling is one of the most important steps towards achieving efficient operations and maximizing profit margins in modern-day manufacturing plants.
Boost Your Manufacturing Business with MPS Technology
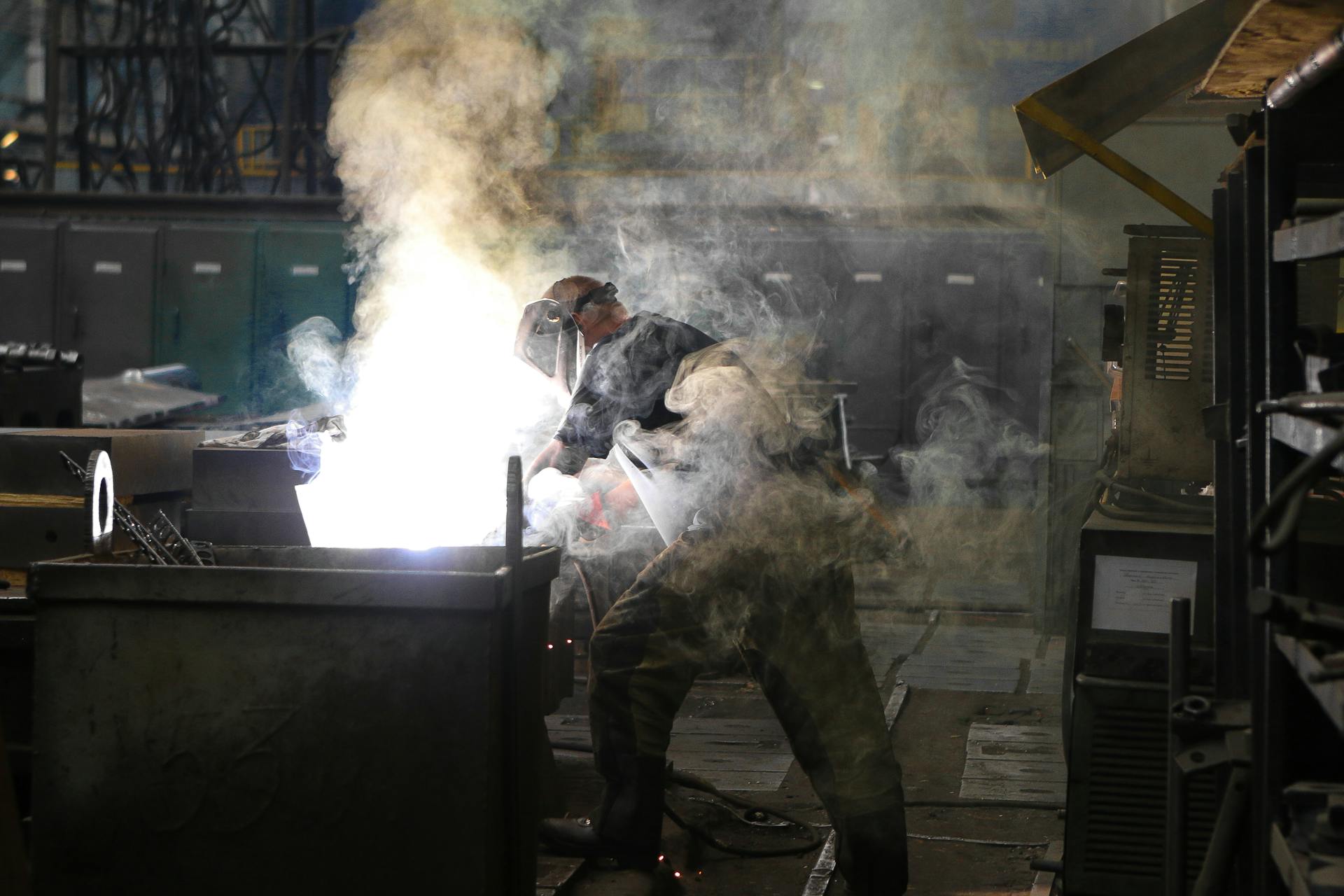
If you're looking to take your manufacturing business to the next level, then implementing a definite MPS is the way to go. MPS fosters a streamlined process, which means reduced production errors and a safer workplace. With clear goals in place, your entire team can work together towards meeting consumer demand consistently.
Implementing an MPS results in efficient companies that follow offers tons of benefits. It promotes healthy business practices, which creates a healthy work culture. A healthier work culture leads to a more productive and motivated workforce that works towards increasing profits for the company.
A definite MPS also helps reduce costs by providing a better understanding of the production process. This understanding allows for adjustments to be made on an ongoing basis. Having access to this knowledge week additionally provides insight into what changes can be made to improve processes further. By implementing an MPS, your manufacturing business will experience significant growth and success!
What Should Be Included in a Master Production Schedule?
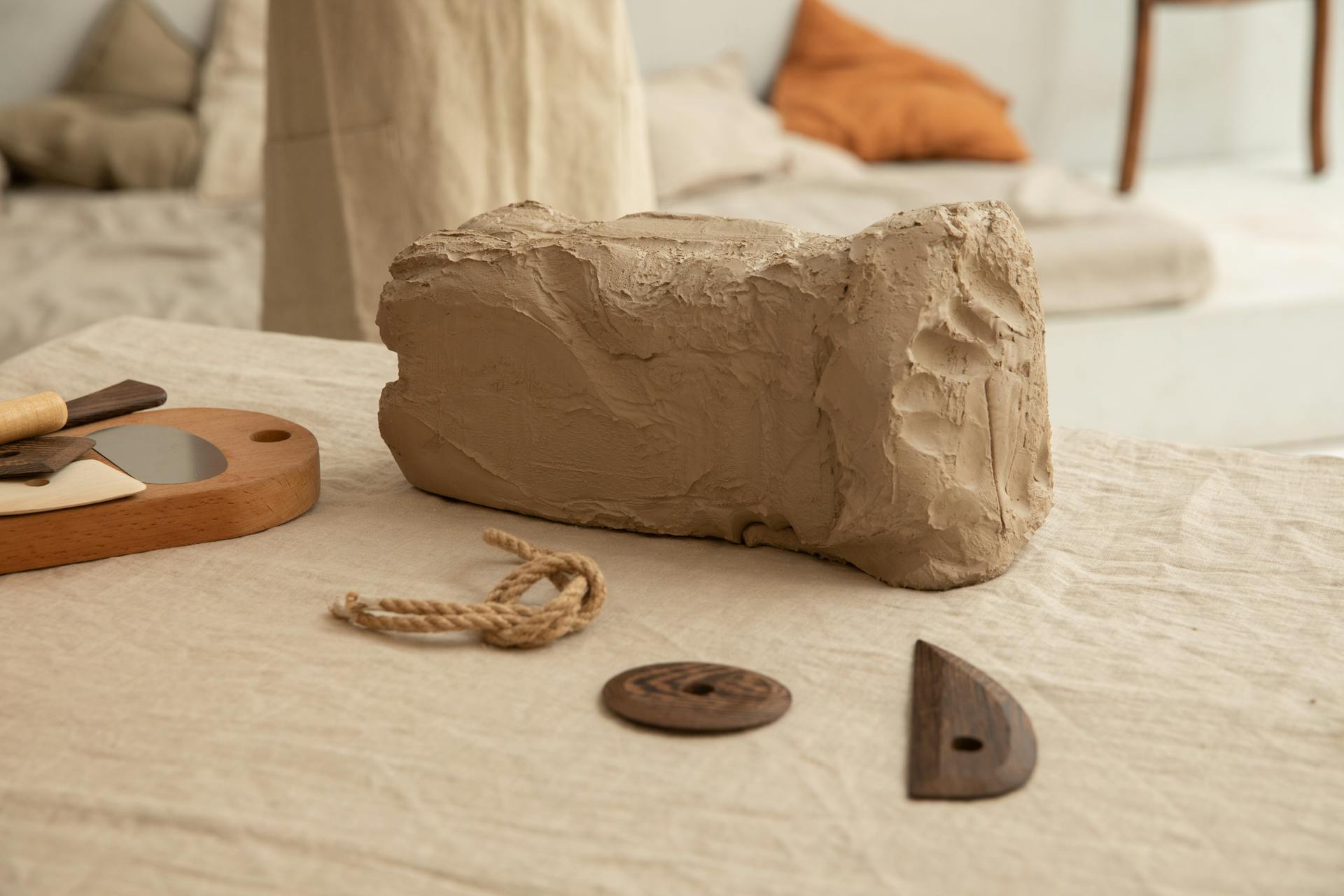
A master production schedule (MPS) is the backbone of any production planning process. It contains critical information about what products will be produced, how much of each product will be made, and when it will be produced. The MPS should include a demand plan that accurately forecasts demand for the coming weeks or months. The demand plan depends on accurate historical sales data and should be regularly reviewed.
What's called "safety stock" should also be stored in the master production schedule. This ensures that in case demand unexpectedly spikes, there is enough inventory to meet customer needs. If you neglect safety stock, you risk losing customers due to stockouts. The master production schedule should contain a product list and variation sublist that accurately forecast demand and production quantities.
It's important to note that the total number of units you're producing should match the total number of units being sold to avoid overproduction or underproduction. A well-designed MPS helps ensure that your business can meet customer demands while keeping inventories at optimal levels. By including all these essential elements in your MPS, you can streamline your production processes and improve overall efficiency.
Maximizing Business Efficiency: Deciding Between MRP and MPS
Common misconception among materials manufacturers is that Material Resource Plans (MRP) and Master Production Schedules (MPS) are interchangeable terms. However, the two are separate documents used during the planning stage to achieve smoother operations. Basically, MRP helps identify the materials present and those required for production while MPS details specific product quantities and delivery schedules. Both MRP and MPS work hand-in-hand to ensure maximum business efficiency.
Shop floor planning and control in production planning
Shop floor planning and control are crucial elements of successful production line discovery. To ensure the smooth functioning of a manufacturing unit, it is important to have an effective shop floor plan in place. This involves the proper allocation of resources and machines, as well as the optimization of time and space. The implementation of a master production schedule can help streamline the process.
Master production schedules are essential business tips for managing production planning. They provide a comprehensive view of all materials required for manufacturing goods, as well as the expected demand for finished products. By having this information readily available, manufacturers can adjust their shop floor planning and control systems accordingly to achieve maximum efficiency.
In conclusion, shop floor planning and control play a vital role in successful production line discovery. The implementation of a master production schedule is an effective business tip for streamlining the manufacturing process. With careful planning and management, businesses can optimize their resources to meet customer demand while minimizing waste and increasing profits.
Discover more: Production Planning
The Benefits of Implementing a Master Production Schedule
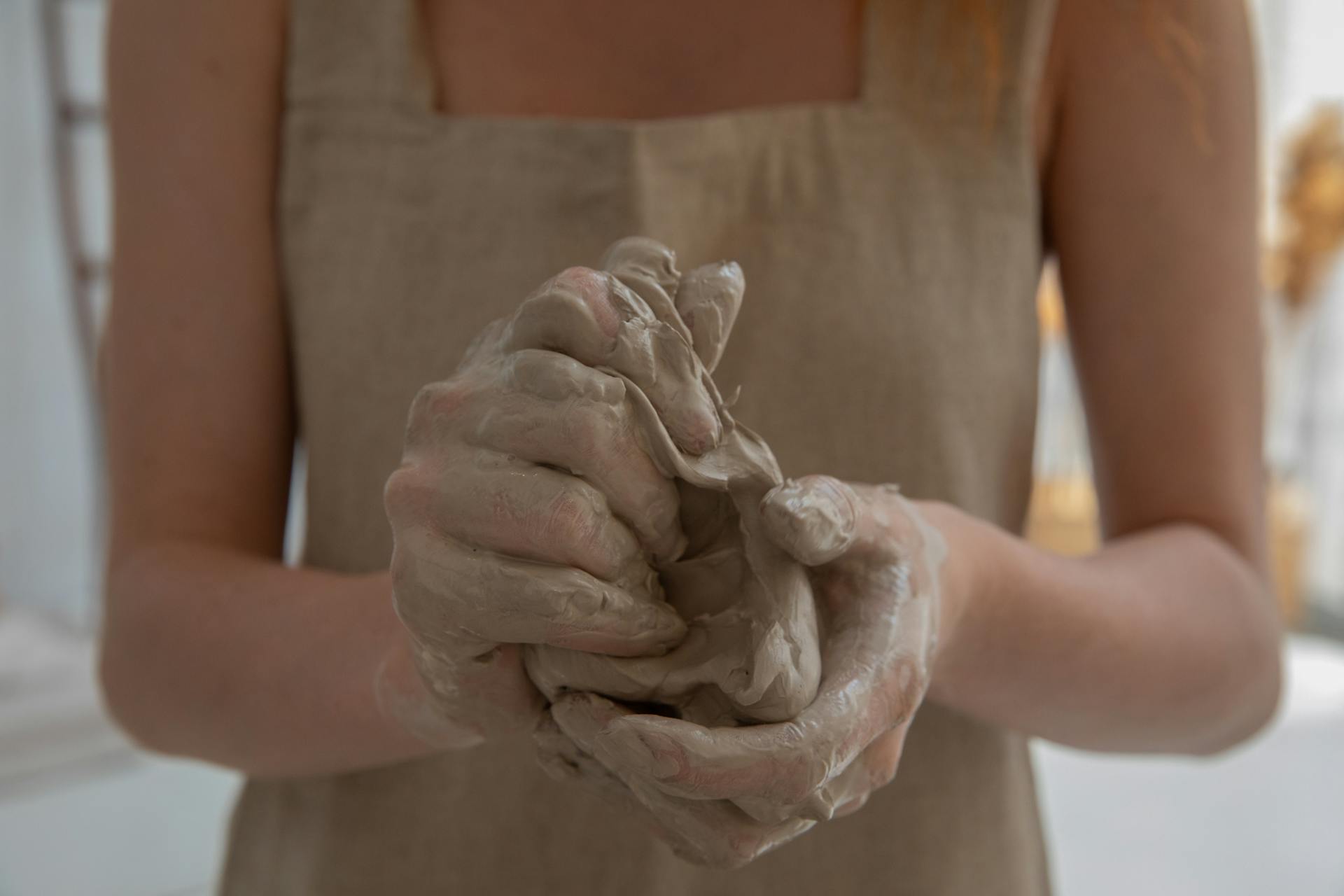
A master production schedule (MPS) serves as the primary purpose of production planning. One of the key important roles that MPS plays is to plan and balance market demand with materials and labor. The main functions of a master production schedule include preventing stockouts by planning ahead, identifying potential efficiencies, and controlling costs. By implementing an MPS, you'll stay in control of your manufacturing process.
The master production schedule process ensures that demand flows smoother, lead times improve, and communication is standardized. This means that unexpected delays are minimized by making adjustments to the schedule schedules. Additionally, capacity requirements can be accurately determined, which helps to improve efficiency and prevent under or overproduction. With an MPS in place, you'll have a better understanding of your customer base manufacturing needs.
By implementing a master production schedule, you can improve efficiency in your company's manufacturing process. You can identify potential efficiencies by analyzing data on materials usage and labor productivity. Standardized requirements enable easier communication across departments, ensuring everyone is working towards the same goals. Overall, implementing an MPS can help control costs while improving overall productivity for your business.
You might like: Production Planning Scheduling
Understanding the Inconsistency of Intermittent Production
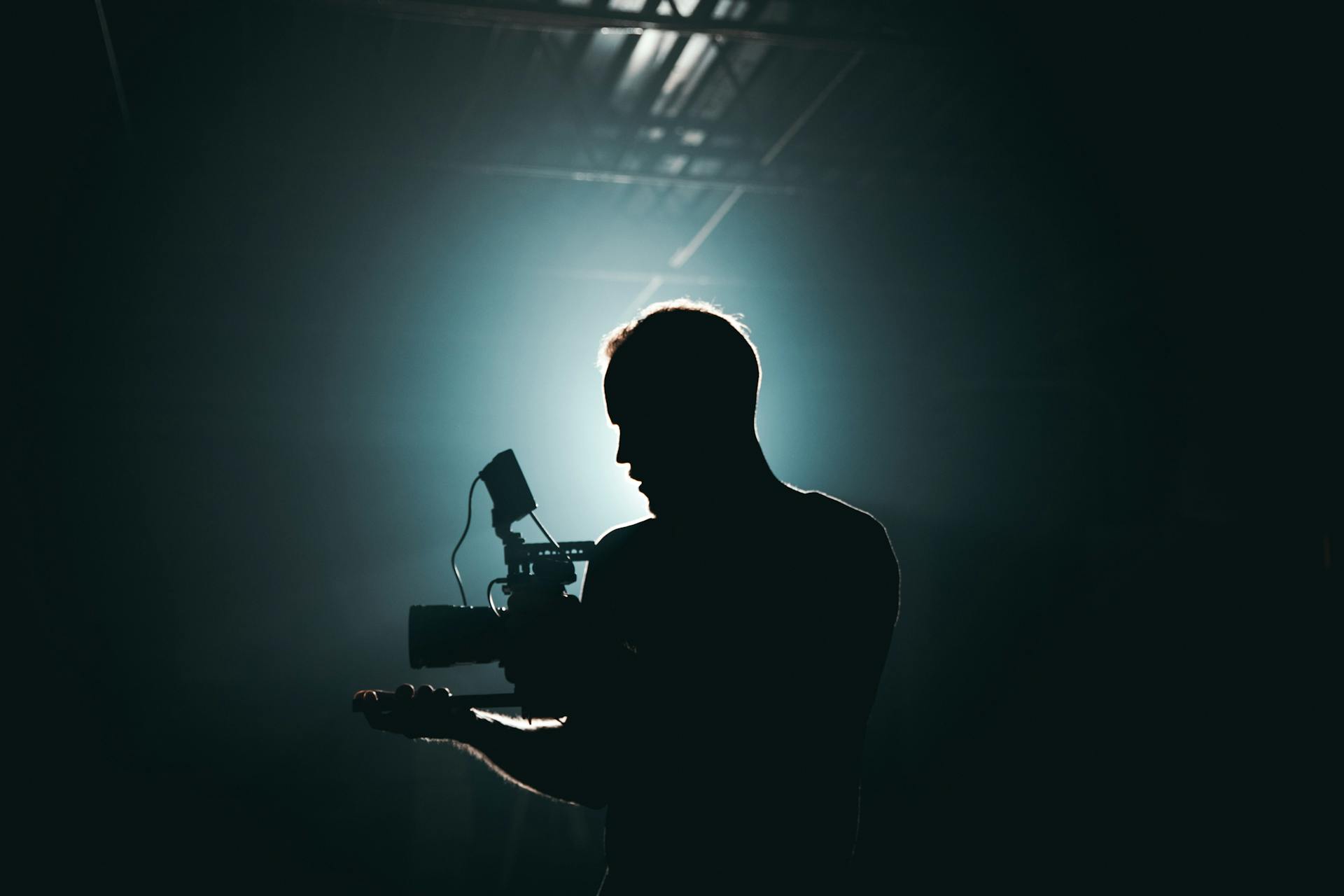
Intermittent production is a production method where products are manufactured in small batches, with each batch being produced separately. This production method is often used for products that have varying demand levels or require specialized manufacturing processes. However, intermittent production can result in inconsistency in product quality and delivery times.
On the other hand, continuous production is a more consistent production method where products are manufactured continuously without interruption. This type of production is typically used for products with high demand levels and standard manufacturing processes. Understanding the differences between these two methods can help businesses make informed decisions about which method to use based on their specific needs. If you're struggling with intermittent production and inconsistent results, it may be time to consider switching to a continuous production model. Keep these business tips in mind as you evaluate your options and strive for more consistent results.
MPS: Why It Matters for Your Business Success
Master production schedules (MPS) are essential for any business looking to achieve its organizational goals. An MPS takes into account the demand plan and outlines how the production process will meet that demand. It is important for team members to work together to create drafts of the MPS, which will require review and refinement until it accurately reflects the needs of the business. By using an MPS, a company can ensure that resources are being used effectively and efficiently, leading to greater success in meeting customer demands and achieving overall business objectives.
Discover the Essential Roles of a Master Production Schedule
The Master Production Schedule (MPS) is a crucial tool for any manufacturing business. The ultimate goal of a master schedule is to ensure that the production flow runs smoothly and efficiently, giving companies the ability to meet demands while minimizing waste. The main objectives of a master production schedule include balancing demand and supply, providing a clear plan for production, and reducing lead times.
One of the most significant advantages of the MPS is the amount of time it can save companies. By spending time managing their master production schedule, businesses can create an accurate forecast of what they need to produce, when they need to produce it, and how much of each product they should manufacture. This helps reduce lead times by ensuring that materials are available when needed, which reduces downtime and increases productivity. Overall, the MPS offers an efficient way for manufacturers to manage their resources effectively and improve their bottom line.
Frequently Asked Questions
What is level production schedule or level schedule?
Level production schedule or level schedule is a manufacturing strategy that aims to produce goods at a constant rate, regardless of demand fluctuations. This approach helps companies avoid stockpiling inventory and reduces the need for overtime or idle time for workers.
How do I create an MPs?
To create an MP, you must first win a seat in the House of Commons by standing as a candidate in a general election. Once elected, you can then begin to represent your constituents and work towards creating legislation.
What is master production schedule?
A master production schedule is a detailed plan that outlines the production schedule for a company, including the quantity and timing of each product. It helps businesses to manage their inventory levels, streamline their production process, and meet customer demand.
How to create a production schedule?
To create a production schedule, first determine the timeline for each task in the production process. Then, allocate resources and assign tasks to team members according to their skill sets and availability. Finally, use a project management tool or software to track progress and make adjustments as needed.
What is an MPs and how does it work?
An MP is a member of parliament who represents a specific geographic area or constituency. They work by debating and passing laws, representing their constituents' interests, and holding the government accountable.
Featured Images: pexels.com