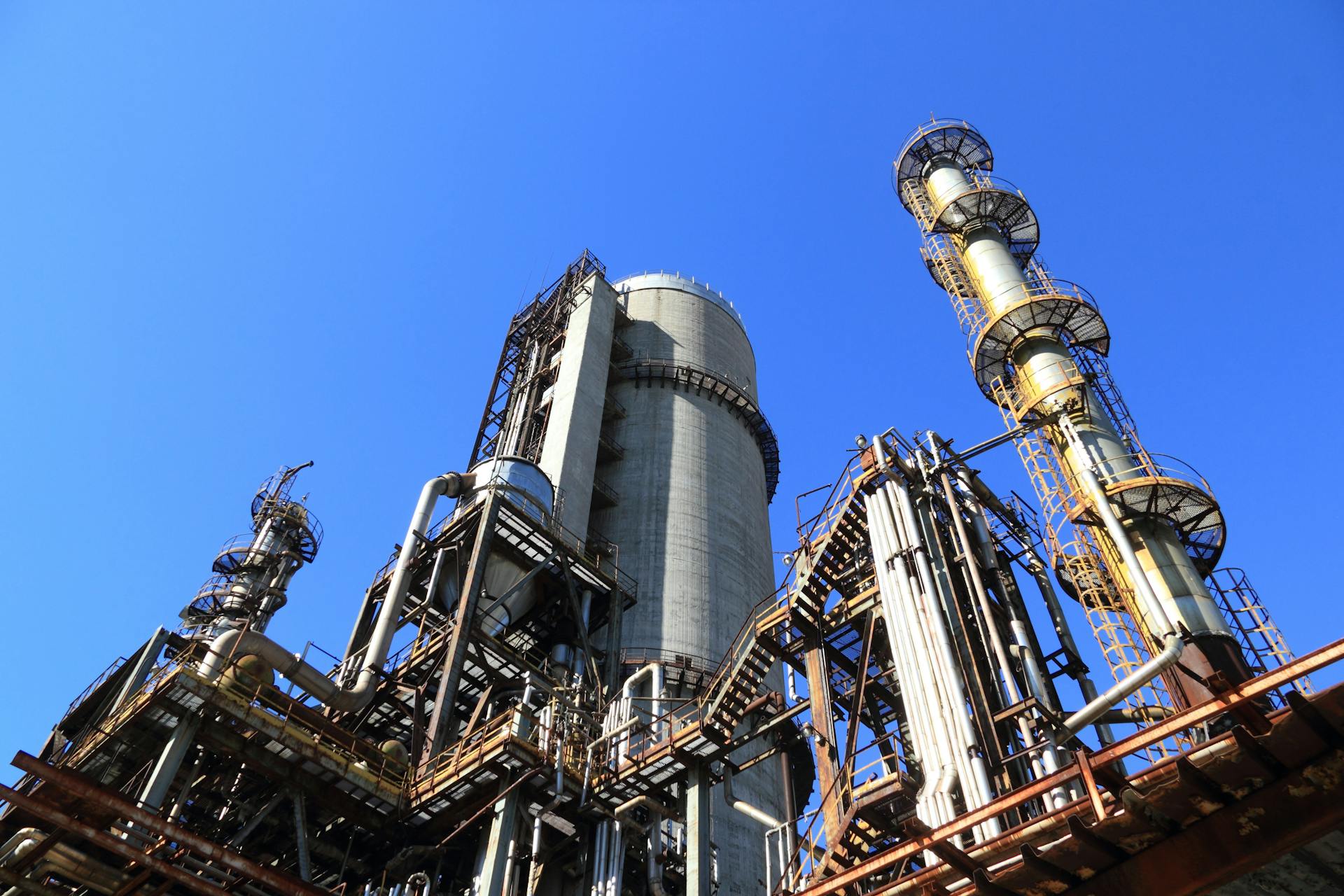
Distributed manufacturing has been gaining steam in North America over the past year as a potential solution to today's supply chain challenges. With parts produced closer to their destination, sudden disruptions such as pandemic-related shutdowns and the global semiconductor shortage can be mitigated. The current system of relying on a complex web of suppliers and manufacturers across the entire world lets dig deeper into why decentralized manufacturing might just be the way of the future.
The COVID-19 pandemic highlighted the fragility of large scale, centralized supply chains. Short supply due to factory closures and shipping delays left many businesses struggling to keep up with demand. However, distributed manufacturing offers a way to build resilience into supply chains by decentralizing production and creating more localized networks. Advancing software solutions also make it easier than ever before to coordinate production and distribution across multiple locations. In this article, we'll explore the distributed manufacturing trend and delve into its advantages over traditional centralized supply chains.
Intriguing read: Production Planning
What is distributed manufacturing?
Distributed manufacturing is the concept of organizing production in a way that makes things closer to where they are needed. Currently, a vast majority of manufacturing industries takes place in centralized locations and products are shipped long distances worldwide to reach consumers. However, with distributed production, we are moving production closer to where it's needed, which can involve setting up small-scale production facilities or using a digital platform.
The goal of organizing distributed manufacturing is to make products designed and manufactured closer to where they will be used. This involves designing products with modular components that can be produced separately using CNC machining techniques and assembly systems. By doing this, we can distribute products locally using 3D printers, plastic injection molding, and other additive manufacturing techniques. This low production cost approach means that finished products can be produced using local resources such as food waste and plastic recycling.
As the world continues to evolve, the common thread driving forces behind distributed manufacturing are the desire for local markets to become self-sufficient while also making an impact on supply chain management. Locations making significant investments in distributed manufacturing will enjoy more access to affordable goods without having to rely on imports from faraway locations. Ultimately, creating these types of localized economies could result in stronger communities and less dependence on external sources for essential goods.
Readers also liked: Production Management
Eliminating Losses in Manufacturing by Improving Quality
In the world of manufacturing, quality should always be a top priority. Poor quality products can lead to a high cost of poor quality (COPQ), which is essentially the amount of money lost due to defects, rework, or scrap. Calculating losses due to COPQ is an essential accounting formula that every manufacturer should know. By improving quality, manufacturers can reduce COPQ and ultimately increase profits.
One way to improve quality is by implementing a distributed manufacturing model. Instead of relying on one centralized location to produce all products, manufacturers can spread out production across multiple locations. This helps reduce the risk of downtime and supply chain disruptions, ultimately leading to better quality control.
Overall, improving quality in manufacturing is crucial for success. Business tips such as implementing a distributed manufacturing model and consistently calculating losses due to poor quality COPQ can help manufacturers eliminate losses and maximize profits.
Here's an interesting read: Manufacturing Quality Control
Costing methods and the importance of choosing the correct one
Costing methods are an essential part of any manufacturing process. Choosing the correct one can significantly impact your business's profit margins. There are two main differences between costing methods: job order costing and process costing. Job order costing is best for custom orders, while process costing works well for mass production.
To improve your profit margin, learn the differences between these two methods and decide which one is best for your specific needs. Understanding both methods will help you make informed decisions about pricing and budgeting. By opting for the right method, you can ensure that your products meet market demands while also reducing waste and costs.
In conclusion, choosing the correct costing method is critical to any successful manufacturing process. Business tips include understanding job order and process costing differences, using them to your advantage, and always working towards optimizing price and budgeting strategies. By implementing these tips and continuously refining your approach, you can ensure that your business maximizes its profits while providing high-quality products to customers.
Recommended read: Purchase Order Process
Distributed manufacturing challenges
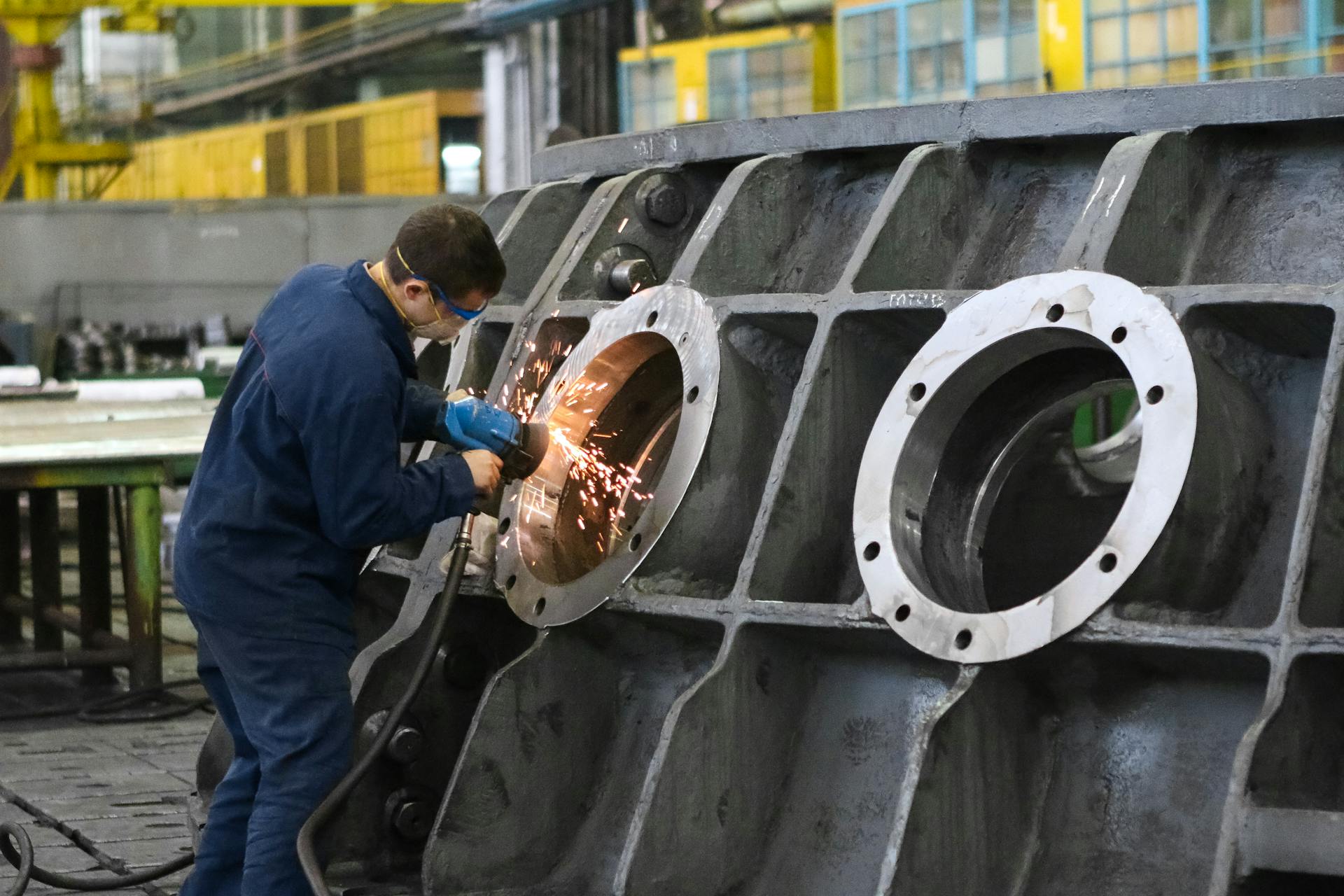
Distributed manufacturing has become a buzzword in the industry as it offers several benefits over traditional centralized manufacturing. However, it also comes with its fair share of challenges. One significant challenge is that distributed manufacturing companies don't provide direct improvement in product quality since production takes place closer to the customer. This makes it difficult to maintain consistency in product standards.
Another challenge is coordinating production and managing inventory levels across multiple locations. Unlike traditional manufacturing, where everything happens under one roof, distributed manufacturing requires careful planning and execution to ensure materials needed for production are readily available at each location. Shipping costs also add up, making it crucial to find ways to reduce the carbon footprint while maintaining efficiency.
Finally, incorporating strong disturbance management is essential for any successful distributed manufacturing system. Additive manufacturing techniques can make local resources accessible for small number production runs, but poor quality or poor production quality can lead to wasted resources and time delays. To overcome these challenges, manufacturers need to have a robust manufacturing strategy that incorporates strong coordination mechanisms and tools that allow them to monitor and manage their operations in real-time accurately.
Here's an interesting read: Manufacturing Lead Time
Discover Agile Manufacturing: A smarter way to produce
You've heard plenty about the traditional manufacturing process, but have you ever heard of agile methodology? Here's a business tip for you: Agile is a smarter way to produce. It's a new and innovative approach that has been gaining popularity in the business world.
Agile manufacturing is all about flexibility, efficiency, and adaptability. This approach allows manufacturers to respond quickly to changing market demands and customer needs. Instead of producing products in large batches, agile methodology focuses on small, iterative cycles of production. This not only reduces waste but also increases responsiveness to changes in customer demand.
In today's fast-paced world, businesses need to be nimble and adaptable. Traditional manufacturing processes can't keep up with the speed of change. That's why more and more companies are turning to agile manufacturing as a way to stay competitive. By embracing this approach, businesses can reduce costs, increase efficiency, and improve customer satisfaction. So if you're looking for ways to improve your manufacturing process, consider adopting agile methodology – it just might be the game-changer you've been looking for!
You might like: Discrete vs Process Manufacturing
Why Distributed Manufacturing is the Future of Production
The current unsustainable model of centralized manufacturing comes with constant threats such as natural disasters, political instability, and trade disputes. This is where distributed manufacturing comes in. The distributed manufacturing model has become popular over the years because it offers many benefits, including the ability to have production happening closer to where the products are needed. By having raw materials and production take place closer to home, we can shorten delivery times and offer leaner manufacturing processes.
One of the main selling points of distributed manufacturing is its ability to improve disturbance handling within the manufacturing system. With a single pod or several smaller ones located in different regions, preventive maintenance can be carried out during short periods without affecting the entire production system. Moreover, this approach makes it possible to customize products depending on local needs, which helps support local economies while creating jobs.
Finally, by embracing distributed manufacturing models, companies can create faster turnaround times for finished products while reducing their carbon footprint. As a result, this approach will likely continue to be universally adopted by companies looking for ways to improve their bottom line while contributing positively to society and the environment.
Frequently Asked Questions
How do you organize distributed manufacturing?
Distributed manufacturing can be organized through the use of digital platforms that connect manufacturers and customers, allowing for efficient communication and collaboration. It also involves implementing standardization processes and utilizing data analytics to optimize production.
How can digital manufacturing reduce the environmental impact of manufacturing?
Digital manufacturing can reduce the environmental impact of manufacturing by optimizing production processes, reducing waste and energy consumption, and enabling the use of sustainable materials. By leveraging digital technologies such as 3D printing, IoT, and AI, manufacturers can achieve greater efficiency and sustainability in their operations.
What is traditional manufacturing?
Traditional manufacturing is the process of using machines and human labor to create products on a large scale. It involves assembly lines, specialized equipment, and standardized processes that have been used for decades.
What is the future of manufacturing?
The future of manufacturing is heavily reliant on automation and digitization. Companies will need to embrace new technologies such as artificial intelligence, IoT, and 3D printing to remain competitive in the global market.
What is distributed manufacturing and how does it work?
Distributed manufacturing is a process where a network of decentralized facilities work together to produce goods. Each facility specializes in one part of the production process, and the finished product is assembled at a centralized location. This allows for greater efficiency, flexibility, and cost savings.
Featured Images: pexels.com